
인공지능 머신러닝을 이용한 체인 스프라켓 드라이브 시스템의 건전성 감시 장치
© The Korean Society for Noise and Vibration Engineering
Abstract
A chain sprocket drive (CSD) system consists of parts such as chains, sprockets, gears, bearings, and rotating shafts. The purpose of this study is to develop a health monitoring system that uses deep learning artificial intelligence (AI) technology to diagnose defects in the CSD system in advance to prevent complete failures due to such defects. In this study, eight types of defects were arbitrarily fabricated and combined to build a CSD system. Deep AI machine learning algorithms were developed to classify and diagnose the eight types of defects. The eight types of defects were mainly limited to bearing parts, gear parts, and rotary shaft parts. Sprocket or chain defects were excluded from the eight types of defects. Finally, an AI machine was successfully developed and applied for diagnosing defects in the CSD system.
Keywords:
Artificial Neural Network, Machine learning, Condition monitoring, Fault diagnosis키워드:
신경회로망, 기계학습, 건전성 감시, 고장진단1. 서 론
체인 스프라켓 드라이브 시스템(이하 ‘CSD 시스템’이라 한다.)는 큰 동력을 필요로 하는 컨베이어뿐만 아니라 엘리베이터, 물류 장비 등 다양한 산업 분야에서 중요한 기계 시스템으로 활용되고 있다. 따라서 CSD 시스템에서 발생하는 결함을 조기에 발견하여 경제적 손실과 인명 피해를 미연에 방지하기 위해 여러 기법들이 연구되어오고 있다. CSD 시스템은 모터, 기어, 피니언, 베어링으로 구성되어 있다. 각 부품의 결함을 진단하기 위해 측정된 진동 신호에 바탕을 두고 있다. 기어와 베어링의 지엽적 결함(local fault)은 갑작스러운 강성 변화에 의한 충격파 진동으로 나타난다(1).
진동 신호로부터 이런 충격파 신호를 찾아내기 위해 kurtosis 평가(2), cepstrum 분석(3), 그리고 신호의 주파수 성분들을 시간 영역에서 동시에 분석하는 시간-주파수 분석법(4,5), 연속 웨이브렛 변환(continuous wavelet transform)(6) 등이 사용되고 있다. 이러한 분석 기법을 통하여 결함과 관계있는 결함 특징을 분석 비교하여 각 결함을 진단하고 결함을 분류하여 건전성감시 시스템을 개발한다(7). 기어 피팅과 회전자 편심같은 피로 결함과 소성변형으로 인한 결함은 충격 신호를 발생시키지 않아 충격파의 특징을 찾아서 결함 부품을 정확히 진단하는 것에 한계가 있다. 이에 이 연구에서는 이러한 한계를 극복하기 위해 단순 주파수분석을 입력으로 하여 딥러닝 알고리듬을 적용하여 높은 분류 정확도를 제공하는 건전성 감시 방법을 제안하고자 한다. 산업 현장에서 많이 발생하고 있는 CSD System 의 결함인 기어 피팅(pitting), 기어 절손(failure), 회전자 편심(eccentricity)의 3가지 단일 결함과 볼 베어링 외륜 구멍, 볼 베어링의 볼 사이 이물질, 회전자 편심 등이 결합된 다중 결함 5가지를 딥러닝 알고리듬에 학습시켜 건전성 감시 실험을 진행하여 딥러닝 기반의 건전성 감시 방법의 유용성을 검증하고자 한다.
2. 실험방법
2.1 실험 장치 및 데이터 수집 과정
이 연구에서 사용되어진 CSD 시스템의 건전성 감시를 위한 CSD 시스템 실험 장치가 Fig. 1에 도시 되어져 있다. 이 실험장치는 0.75 kW의 MSS-080M DC모터와 2개의 기어 축 및 베어링으로 연결되어 모터의 회전비를 감속하여 체인을 구동하는 시스템이다. 입력 축 회전 속도는 DC모터에 연결되어진 DC속도 조절기(DC speed controller)로써 조절이 가능하고 체인의 구동 초기 관성에 의한 부하가 존재하지만 외부 부하는 없다.
이 실험에서는 1800 r/min의 입력 축 회전 속도와 감속기를 통과 후에는 30배 감속하여 60 r/min 으로 체인을 구동 시킨다. 이 실험을 위해서 기어, 베어링, 및 축에 인위적인 결함을 만들어 제작 후 조립하여 각 실험을 수행하였다. 결함의 타입은 기어 피팅, 기어 절손, 회전자 편심의 3가지 단일 결함과 볼 베어링 외륜 구멍, 볼 베어링의 볼 사이 이물질, 회전자 편심 등이 결합된 다중결함 5가지로 하였으며 이에 의한 진동 신호를 얻기 위해 가장 근접해 있는 베어링 하우징(bearing housing) 상단에 가속도계(accelerometer; B&K 4366)를 부착하였다. 가속도계에서 측정된 진동 신호는 증폭기(amplifier)를 통하여 증폭시키고 DAQ 보드(BNC-2090)를 이용하여 엔지얼라이징 필터를 통과 후에 아날로그를 디지털로 변환 후 컴퓨터 전달되었다. 컴퓨터에 수집된 디지털 신호는 Matlab (MathWorks사, 미국)을 활용하여 신호를 처리하고, 분석하여, 건전성 감시 알고리듬을 개발하였다.
2.2 CSD 시스템의 결함 형태 및 위치
기어 상단 부분의 절손은 기어 파손 중 실제 산업 현장에서 많이 발생되는 형태 중 하나이다(8,9). 이런 파손은 순간적인 과부하(overload) 또는 구조물의 부적절한 설치(misalignment), 베어링 파손, 큰 이물질의 침투 등으로 인한 굽힘 피로의 누적으로 비교적 큰 금속편이 치면으로부터 박리하는 손상으로 조립이나 제조 과정 등에서도 발생될 수 있다.
Fig. 2는 이 실험에서 사용되어진 정상 기어와 지협적 결함을 갖는 기어의 형상을 나타내고 있다. Fig. 2의 (b)는 상단 절손을 갖는 기어를 실험용으로 제작한 것으로 기어 작용높이(working depth)의 25 %를 0.5개 너비만큼 줄(file)로써 제거해 주었다. 이와 같은 결함을 가지는 기어를 전체 82개 중 42번째에 위치시켜 기어의 결함을 탐지하는 기어 시스템의 건전성 감시 실험을 실시하였다.
기어 피팅은 일반적인 기어 결함(fault) 중 하나이다. 이러한 결함은 설계 하중보다 높은 부하, 부적절한 표면처리, 열악한 작동 조건 등으로 기어 이의 표면이나 표면 아래의 낮은 깊이에서 피로 균열이 시작된다. 100 μm ~ 500 μm 또는 더 깊은 영역에서 접촉하중에 의해 생성된 전단응력이 균열을 빠르게 성장시키고 전파시키며 큰 조각이 치면으로부터 박리되어 큰 구멍을 남긴다(10,11).
Fig. 3은 이 실험에서 사용되어진 정상 기어와 지협적 결함을 갖는 기어의 형상을 나타내고 있다. Fig. 3의 (b)는 표면에 피팅을 갖는 기어를 실험용으로 제작한 것으로 기어 작용 높이(working depth)의 5 %를 부분적으로 줄(file)로써 제거해 주었다. 이와 같은 결함을 가지는 기어를 전체 82개중 41, 42, 43번째에 위치시켜 기어의 결함을 탐지하는 기어 시스템의 건전성 감시 실험을 실시하였다.
회전자 편심은 유도전동기의 고장의 원인 중 큰 비중을 차지한다. 이러한 결함은 부적절한 결합(misalignment), 베어링의 마모, 샤프트의 소성변형 등으로 인해 발생한다. 회전자 편심으로 인해 자속분포의 불균형이 발생하고 unbalanced magnetic pull(UMP)이라는 불균형 가진력을 유발시켜 베어링 마모, 고정자 권선의 손상 등의 고장을 발생시킨다(12).
Fig. 4은 이 실험에서 사용되어진 정상 회전자와 편심된 회전자의 형상을 나타내고 있다. Fig. 4의 (b)는 편심된 회전자를 실험용으로 제작한 것으로 회전 중심으로부터 원주방향으로 10 mm가 편심되어있다. 이와 같은 결함을 가지는 회전자를 결합하여 회전자 결함을 탐지하는 CSD 시스템의 건전성 감시 실험을 실시하였다.
베어링 볼 사이의 이물질은 조립과정에서 칩을 완벽하게 세척하기 못했거나 지속적인 운전으로 인한 마멸입자(wear debris)로 인해 발생한다. 볼 사이의 이물질은 구름접촉면을 손상시켜 베어링의 피로수명을 현저하게 감소시킨다(13)(14).
Fig. 5은 이 실험에서 사용되어진 정상 볼 베어링과 볼 사이에 이물질을 갖는 볼 베어링의 형상을 나타내고 있다. Fig. 5의 (b)는 볼 사이의 이물질을 투입한 볼 베어링을 실험용으로 제작한 것이다. 이와 같은 결함을 가지는 볼 베어링을 CSD 시스템에 결합하여 베어링의 볼 결함을 탐지하는 CSD 시스템의 건전성 감시 실험을 실시하였다.
베어링 고장(failure)은 산업 기계에서 가장 흔한 결함 중 하나이다. 특히 회전기기의 고장 원인에서 베어링의 손상이 큰 비율을 차지하고 있다(15). 이러한 결함은 과도한 부하(overload), 부적절한 기기 운전이나 피로로 인해 외륜에 흠집이 나타나는 박리 손상으로 장시간 운전할 경우 베어링 온도가 상승하여 소착되고 큰 사고로 이어질 수 있다(16).
Fig. 6은 이 실험에서 사용되어진 정상 볼 베어링과 외륜에 구멍을 갖는 볼 베어링의 형상을 나타내고 있다. Fig. 6의 (b)는 외륜에 구멍을 내어 볼 베어링을 실험용으로 제작한 것이다. 이와 같은 결함을 가지는 볼 베어링을 CSD 시스템에 결합하여 베어링의 외륜 결함을 탐지하는 CSD 시스템의 건전성 감시 실험을 실시하였다.
단일 부품의 결함으로 인해 불균형 가진력이나 충격 신호가 발생하고 이를 인지하지 못한 상태에서 운전이 지속되면 베어링, 기어 등 주변 부품으로의 다중 결함을 유발하는 경우가 발생한다. 따라서 다중 결함의 신호를 확보하여 학습 후 결함 부품의 종류를 정확히 분류할 필요가 있다. 다중 결함을 가지는 CSD 시스템의 실험은 결함을 갖는 단일 부품을 CSD 시스템에 결합 후 실험하여 신호를 측정하였다.
Table 1은 CSD 시스템의 단일 결함 및 다중 결함을 갖는 부품의 종류를 나타낸다. 빈칸은 정상 부품이 결합됨을 나타낸다.
3. 신호처리
3.1 고속 푸리에 변환
푸리에 변환은 시간 축에서 측정된 신호를 주파수 축으로 변환시켜준다. 고속 푸리에 변환(fast Fourier transform)은 이산 푸리에 변환(discrete Fourier transform, DFT)을 빠르게 수행하는 기법이다(15). 고속 푸리에 변환을 적용하여 결함 주파수의 확인 등 주파수 영역의 정보를 확인할 수 있다(식 (1)).
(1) |
3.2 PSD 이론
랜덤 진동의 진동 해석에서 효과적인 주파수 분석 기법으로 신호의 파워를 주파수 축에서 주파수 별 분포로 나타낸다. PSD (power spectral density)는 식 (2)와 같이 통계적인 방법으로 정의된다.
(2) |
3.3 CSD 시스템의 진동 신호의 주파수분석
Fig. 7은 정상 부품이 결합된 CSD 시스템의 x축의 진동 FFT 그래프이고 Fig. 8는 절손 된 기어가 결합된 CSD 시스템의 x축 진동 FFT 그래프이다. 또한 Fig. 9는 teeth pitting을 가지는 기어가 결합된 x축 진동 FFT 그래프를 나타낸다.
절손된 기어가 결합된 경우 충격 신호가 발생하여 기어의 맞물림 주파수인 449 Hz에서 높은 진동가속도가 확인된다. 따라서 기어 절손으로 인한 결함 주파수임을 확인하여 결함을 기어 절손으로 분류할 수 있다. 그러나 기어 피팅이 발생한 부품이 결합된 경우Fig. 9에서 결함 주파수의 높은 가속도같은 뚜렷한 고장의 양상을 확인하기 어려워 결함 부품의 분류가 어렵다.
4. 신경회로망을 이용한 분류기 개발
Fig. 10은 한 개의 뉴런(neuron)에서 입력 x와 출력 y의 관계를 나타낸다. 한 개의 층(one layer)을 갖는 신경회로망은 식 (3)과 같이 표현된다.
(3) |
입출력 관계가 복잡한 문제를 해석하기 위해서는 일반적으로 Fig. 11과 같은 다층 신경회로망을 사용하며 식 (4)와 같이 표현된다.
(4) |
식 (3), (4)에서 X=[x1 x2 … xp]T는 입력벡터, Y=[y1 y2 …yn]T는 출력 벡터, f는 전달함수(transfer function), W는 가중치(weight) 행렬을 나타낸다.
이 연구에서는 입력층 (input layer)에는 233개 입력 뉴런, 은닉층 (hidden layer)에서는 110개의 뉴런을 사용하였고 출력층 (output layer)에는 결합의 종류를 나타내는 9개의 뉴런을 갖는 신경회로망을 구현하였으며, 결함 분류를 위해서 출력층에는 softmax 함수를 적용하였다.
신경 회로망의 입력 값으로 x축, y축, z축 진동에 단시간 푸리에 변환(short time Fourier transform)을 적용하여 얻어진 FFT data를 사용하였고 목표 값으로 고장번호를 one-hot in coding방식으로 변환하여 적용하였다. 2096개의 70 %인 1468개의 FFT data를 신경회로망 학습과정에 사용하여 최적화된 가중치 행렬 W를 구하였다. 나머지 30 %는 validation과 test에 각각 15 % 식 314개를 사용하였다. Fig. 12부터 Fig. 20의 target은 one-hot in coding 된 고장번호이며, test는 최적화된 신경회로망을 이용하여 계산된 출력 값이며 target 기호와 test 기호가 일치하는 것은 정확한 분류를 나타낸다. 각 데이터의 target 값이 1이면 각 해당 조건에 대한 결함을 나타내며, 0 이면 다른 조건에 대한 결함을 나타낸다. Fig. 12부터 Fig. 20까지 target 값과 test 값이 각 해당 조건에 잘 일치하여 해당결함이 95 % 이상 탐지 됨을 알 수 있다.
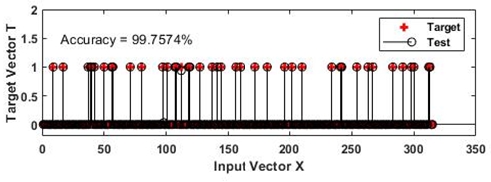
Classification of vibration data measured in x-direction for the CSD system with multiple defect 4 in Table 1
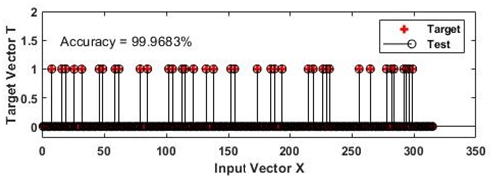
Classification of vibration data measured in x-direction for the CSD system with multiple defect 5 in Table 1
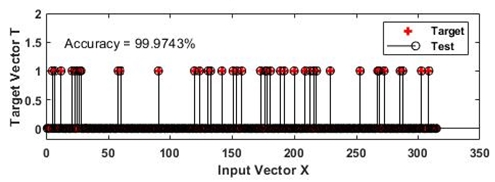
Classification of vibration data measured in x-direction for the CSD system with multiple defect 6 in Table 1
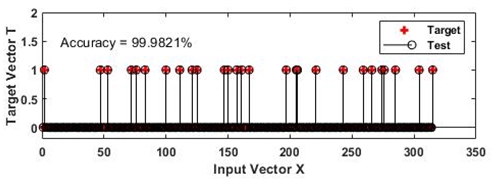
Classification of vibration data measured in x-direction for the CSD system with multiple defect 7 in Table 1
실제 고장번호와 신경회로망의 출력 값은 Table 2와 같이 평균 98.7 %의 정확도를 나타낸다.
CSD 시스템의 건전성 감시 실험 결과 여러 축의 진동 신호 중 가장 정확도가 높은 X축의 진동 신호를 이용하는 것이 바람직하다.
5. 결 론
CSD 시스템의 건전성 감시 방법으로서 이 연구에서는 신경회로망을 이용하는 방법을 제안하였다. 신경회로망의 입력 값으로 결함 종류에 따른 FFT data를 사용하였고 목표 값으로 one-hot in coding방식의 고장번호를 사용하였다. 학습과정을 통해 최적화된 신경회로망의 출력 값은 실험에 사용된 315개에 대해 평균 98.8%의 정확도를 나타냄으로써 CSD 시스템의 건전성 감시에 사용될 수 있음을 확인하였다.
단일 결함 및 다중 결함을 갖는 CSD 시스템에 대한 건전성 감시 실험을 통해 충격 신호뿐만 아니라 일반적인 신호를 가지고 있는 CSD 시스템의 건전성 감시에 있어 이 연구에서 제시한 신경회로망을 이용한 고장 분류 기법이 탁월한 유용성이 있음을 검증할 수 있었다.
References
- Lee, S. K. and Sim, J. S., 2009, Condition Monitoring in Gear System Using Spike Wavelet Transform, The Acoustical Society of Korea, Vol. 20, No. 5, pp. 21~27.
-
Dyer, D. and Stewart, R.M., 1978, Detection of Rolling Element Bearing Damage by Statistical Vibration Analysis, Journal of Mechanical Design, Vol. 100, No. 2, pp. 229~235.
[https://doi.org/10.1115/1.3453905]
- Randall, R., 1982, Cepstrum Analysis and Gearbox Fault Detection, B&K Application Note, Technical Report, pp. 13~150.
-
Lee, S. K. and White, P. R., 1997, Higher-order Detection in Rotating Machinery, Mechanical System and Signal Processing, Vol. 11, No. 4, pp. 637~650.
[https://doi.org/10.1006/mssp.1997.0098]
-
Lee, S. K. and White, P. R., 1999, Two-stage Adaptive Line Enhancer and Sliced Wigner Trispectrum for the Characterization of Faults from Gear Box Vibration Data, Journal of Vibration Acoustics, Vol. 121, pp. 488~494.
[https://doi.org/10.1115/1.2894007]
-
Boulahbal, D., Golnaraghi, M. F. and Ismail, F., 1999, Amplitude and Phase Wavelet Maps for The Detection of Cracks in Geared Systems, Mechanical System and Signal Processing, Vol. 13, No. 3, pp. 423~436.
[https://doi.org/10.1006/mssp.1998.1206]
- Braun, S. G., Ewins, D. J. and Rao, S. S., 2002, Encyclopedia of Vibration, Academic Press, pp.143~150, pp. 597~603.
- Staszewski, W. J., 1994, The Application of Time-variant Analysis to Gearbox Fault Detection, PhD Dissertation, Manchester University, pp. 109~117.
-
Lee, S. K., 1999, Application of the L-wigner Distribution to the Diagnosis of Local Defects of Gear Tooth, KSME International Journal, Vol. 13, No. 2, pp. 144~157.
[https://doi.org/10.1007/BF02943666]
-
Liang, X. H., Liu, Z. L., Pan, J. and Zuo, M. J., 2017, Spur Gear Tooth Pitting Propagation Assessment Using model-based Analysis, Chinese Journal of Mechanical Engineering, Vol 30, No. 6, pp. 1369~1382.
[https://doi.org/10.1007/s10033-017-0196-z]
- Kalathur Kumar, D. S., Sriram, G., Mani, V. N. and Kumar, V. P., 2016, Investigating of Pitting Formation on Gear Tooth and Evaluating Life Time of Gears Using Sem, Vol. 3, No. 6, pp. 96~103.
- Frosini, L. and Pennacchi, P., 2004, Detection and Modelling of Rotor Eccentricity in Electrical Machines: an Overview, IMechE Event Publications, Vol. 1, No. 2, pp. 501~510.
-
Baek, H. Y., Pyun, J. M., Lee, D. Y. and Park, T. J., 2015, Improving the Endurance Life of Deep Groove Ball Bearings for Automotive Transmission, Tribology and Lubricants, Vol. 31, No. 6, pp. 281~286.
[https://doi.org/10.9725/kstle.2015.31.6.281]
- Im, J., Choi, Y., Kim, S., Kim, T and Im, J., 2015, Development of Early Monitoring System of Bearing Fatigue Defection of a Shaft in Railway Vehicle, Proceedings of 2015 Spring Conference in the Society of Korea Railway, pp. 294~297.
- Kumbhar, A. J. and Chhapkhane, N. K., 2014, Detection of the Distributed Defects on Inner & Outer Race of Ball Bearing using Vibration Analysis, International Journal of Engineering Research & Technology, Vol. 3, No. 11, pp. 147~150.
- R. H. Jeoung,, Lee B. G. and Lee, D. H., 2010, Study on Detection Technique for Outer-race Fault of the Ball Bearing in Rotary Machinery, Journal of The Korean Society of Safety, Vol. 25, No. 5, pp. 1~6.
-
Heideman, M., Johnson, D. and Burrus, C., 1984, Gauss and the History of the Fast Fourier Transform, IEEE ASSP Magazine, Vol.1, No. 4, pp. 14~21.
[https://doi.org/10.1109/MASSP.1984.1162257]
- Davies, P. and Laux, P. D., 2000, Artificial Neural Network Modeling of Human Response to Synthesized Machinery-like Sound, Proceedings of the 7th International Congress on Sound and Vibration, Garmisch-Partenkirchen, Germany, pp. 2461~2468.
- Lee, S. K., Chae, H. C., Park, D. C. and Jung, S. G., 2002, Sound Quality Index Development for the Booming Noise of Automotive Sound Using Artificial Neural Network Information Theory, Proceedings of the Inter-Noise and Noise-Con Congress and Conference, Vol. 2002, No. 1, pp. 35~40.
- Dai, Y., Lim, T. C. and Karr, C. L., 2002, Neural Network Simulation of Subjective Response to Brake Squeal Noise, Proceedings of the Inter-Noise and Noise-Con Congress and Conference, Vol. 2002, No. 1, pp. 65~70.
Jiseon Back is a graduate student in Department of Mechanical Engineering at Inha University. He has studied for the application of signal processing to automotive sound quality and active noise control.
Seon-Won Kim is a graduate student in Department of Mechanical Engineering at Inha University. He has studied for the application of signal processing to the ride quality analysis of a vehicle and the health monitoring of mechanical system.
Sang-Kwon Lee studied in the Department of Mechanical Engineering at the Pusan National University, Pusan, Korea for B.S. In 1998, he received a Ph. D degree in signal processing at the ISVR (Institute of Sound and Vibration Research) of the University of Southampton in U.K. He has continued the sound and vibration research in the department of mechanical engineering inha University since 1999. He worked in Hyundai Motor Company between 1984 and 1994 and researched Samsung Motor Company on 1998.