
추진축과 스트러트 베어링 간 스틱슬립 비선형 마찰진동으로 인해 발생한 이상소음의 분석
‡ Recommended by Editor Won Ju Jeon
© The Korean Society for Noise and Vibration Engineering
Abstract
When the propulsion shaft is rotating, friction-induced vibrations can occur between the shaft and bearing according to the lubrication condition. For ship applications, a water-lubrication bearing is usually adapted at the strut structure where the bearing is located in the water. Because the strut bearing is lubricated with seawater, the friction coefficient is greater than that for the oil-lubricated bearing and the friction coefficient varies as an exponential function of the relative velocity from the shaft to the bearing. Under this condition, the shaft system can become unstable and stick-slip nonlinear friction-induced vibration can occur. In this research, the abnormal noise caused by the stick-slip motion between the propeller shaft and strut bearing is described. Through experiment and analysis, it can be verified that the abnormal noise is caused by the stick-slip vibration.
Keywords:
Stick-slip Nonlinear Vibration, Self-excited Vibration, Strut Bearing, Rope Guard키워드:
스틱슬립 비선형진동, 자려진동, 스트러트 베어링, 로프 가드1. 서 론
최근 새로운 함정의 건조가 활발히 이루어지면서 설계단계에서 검증하지 못했던 이상소음 문제가 자주 발생하고 있다. 특히 추진축 쪽에서 발생하는 이상소음은 유동, 마찰 등 비선형 진동에 의해 발생되는 사례가 늘고 있으며 이러한 이상소음 및 진동은 추진시스템의 베어링 손상, 축의 피로파손 등 치명적인 손상을 야기할 수 있으므로 이에 대한 원인규명을 정확히 수행하고 이를 충분한 수준으로 저감 또는 소멸시켜야만 한다.
Simpson, T. A. et al.(1)은 축과 베어링을 컨베이어 위에서 스틱슬립 운동을 하는 물체와 동일한 운동을 한다고 가정하고 회전속도에 따른 마찰력의 변화가 음의 관계를 가지는 경계윤활영역 및 혼합 윤활영역에서 스틱슬립에 의한 마찰진동 및 추진축계의 안정도문제를 다루었다. Bhushan, B.(2)는 실험실에서 시편시험을 통해 해수윤활 베어링에서 발생하는 스틱슬립 현상을 분석하였으며 베어링에 작용하는 수직력, 축의 회전수, 베어링의 표면상태 및 재질을 변경해 가면서 스틱슬립에 의한 비선형 마찰진동을 평가하였다. Peng, E. et al.(3)은 고무 재질의 해수윤활베어링에 대해 수압 및 온도 변화에 따른 동마찰계수를 평가하였고 Albers, A. et al.(4)은 자동차 클러치에서 발생되는 채터링(chattering) 소음의 발생원인이 특정속도에서 클러치판에 작용하는 수직력 변화에 따른 스틱슬립 마찰진동임을 파악하였다. Han, H. S. et al.(5)은 축-베어링계를 2 자유도계로 가정하고 수직하중 및 댐핑변화에 따른 스틱슬립 발생여부를 예측하였으며, 실선실험을 통한 스틱슬립 발생 및 개선사례를 소개하였다.
이러한 스틱슬립 현상에 의한 마찰진동이 크게 발생할 경우 베어링의 마모 또한 크게 발생될 수 있으므로 마모와 연관한 마찰진동의 연구도 활발히 이루어지고 있다(6~8).
이 연구에서는 특정함정에서 발생한 이상소음이 축-베어링간 스틱슬립에 의해 발생한 것으로 추정되어 이를 스틱슬립 비선형 마찰진동 관점에서 분석하고자 한다. 이 연구에서 다루는 함정의 이상소음은 회전수와 관계없이 특정주파수에서 발생하고 있었으며, 이후 함속을 증가시키거나 감소시키면 이 소음이 갑자기 사라짐을 알 수 있었다. 이러한 현상은 전형적인 자려진동의 형태이며 상대적으로 저속조건에서 발생됨에 따라 스틱슬립에 의한 비선형 마찰진동에 의해 이러한 이상소음이 발생한 것으로 추정되었다. 따라서 함미에서 이상소음이 발생할 때 함미부 및 축계에 가속도계를 부착하고 이를 통해 수집된 진동 스펙트럼 분석을 통해 회전수와 관계없이 나타나는 진동 성분에 대한 원인을 분석하였다.
2. 이상소음 발생조건에서의 진동 계측
이 연구에서 다루는 함정에서 발생하는 이상소음을 평가하기 위해 Fig. 1과 같이 함미 타기실 선체 및 추진축 베어링 하우징에 가속도계를 부착하고 함속력 및 추진축 회전수 변화에 따른 선체 및 추진축계 진동을 확인하였다.
가속도계의 경우 승조원으로부터 함미 타기실의 스트러트 연결부에서 이상소음이 가장 크게 발생되는 것으로 파악되어 좌우현 V-스트러트 지지 연결 선체에 3축 가속도계(356A02(PCB))를 부착하여 이상소음 발생 시 선체에 전달되는 진동 신호를 데이터 수집장치(type 3053-B-12/0 (B&K))를 통해서 계측하였다. 일반적으로 진동의 가진력은 축계에서 발생하므로 접근 가능한 추진축 중간 라인베어링 및 추력베어링 하우징에 축방향 및 반경방향으로 단축 가속도계(352C03(PCB))를 추가로 부착하였다. 축 회전수는 타코메터(A2103/LSR/001 (compact instrument))를 이용하여 함 속력 단계별로 계측하였다.
진동 계측은 함 직진항해 시 함속이 안정된 이후 계측하였으며 이상소음이 크게 발생하는 조건에서는 함 선회 시(5도 선회) 진동을 추가적으로 계측하였다. 함 속력은 PCL(power control level)로 미리 설정하여 운항하고 있으며 축 회전수는 96 r/min ~ 160 r/min의 범위 내에서 PCL 10부터 PCL 100까지 설정되어 있다.
시험결과 함 속력이 PCL 35조건이 되면 좌현부에서 이상소음이 갑자기 발생하기 시작하여 지속되다가 PCL 60부터는 갑자기 이상소음이 사라짐을 알 수 있었다.
Fig. 2는 이상소음 발생 시 함 속력별 좌우현 함미 타기실 V-스트러트 연결부 선체에서 계측한 선체 수직방향의 진동 스펙트럼이다. Fig. 2(a) 좌현(PORT) 진동 스펙트럼으로부터 이상소음이 발생하는 PCL 35 ~ PCL 55에서는 f1 Hz 및 이의 조화성분이 축방향, 횡방향 및 수직방향 모두 발생하고 있음을 알 수 있으며 이들 진동 성분은 축회전수와 관계없이 동일한 주파수에서 큰 토널(tonal) 성분을 가지고 있음을 알 수 있다. 하지만 우현(STBD)의 경우 모든 조건에서 특이한 진동 성분이 발견되지 않으며 PCL 35 ~ PCL 55 조건에서 좌현대비 완전히 다른 진동 스펙트럼을 보여주고 있다. 반면 Fig. 2(b)의 진동 스펙트럼으로부터 PCL 10 ~ PCL 30, PCL 60 ~ PCL 100 구간에서는 좌우현 모두 이러한 진동 성분이 없으며 좌우현간 진동 스펙트럼 차이 또한 크지 않음을 알 수 있었다. 따라서 진동 시험 결과 이들 이상소음은 좌현에서 발생하고 있음을 알 수 있다.
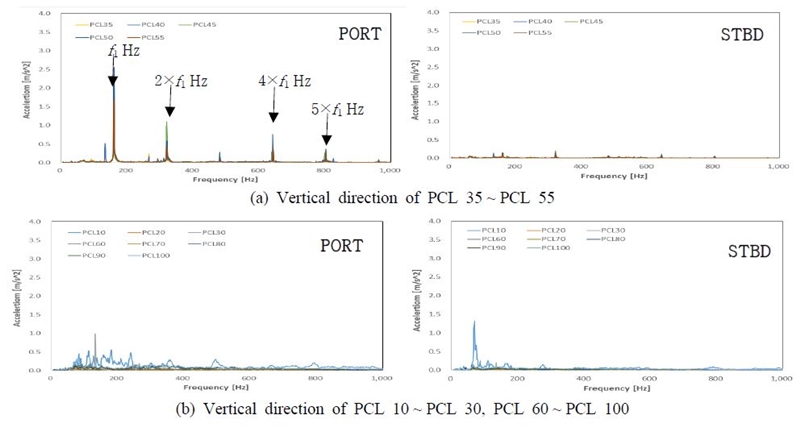
Acceleration spectra measured on the strut supported structure according to the propulsion shaft speed variation
계측결과 소음발생 시 이상소음의 주파수가 회전수에 따라 변하지 않기 때문에 회전체의 불평형력 등 가진력에 의해 특정 진동모드가 가진되는 현상은 아닌 것으로 판단되었다.
이상소음을 야기시키는 진동의 발생원인이 추진축이라면 추진축의 어느 위치에서 어떠한 진동이 발생하는지 파악해야하며, 이를 확인하기 위해서 중간축 라인베어링과 추력베어링 하우징에서의 진동을 축방향 및 반경방향에 대해 계측하였다.
계측결과 라인베어링과 추력베어링에서는 회전수 변화에 따라 특이한 진동성분은 발견되지 않았다.
따라서 진동 계측 결과로부터 이 이상소음의 발생은 좌현 추진축계의 문제로 인해 발생하고 있음을 예측할 수 있으며 특히 함미 스트러트베어링 쪽에서 발생되었을 가능성이 높다고 판단되었다.
이 연구에서 다루는 함정의 V 및 I-스트러트 베어링의 경우 수윤활 베어링으로 윤활막이 충분하게 생성되지 못하는 저속 조건에서 비선형 스틱슬립(stick-slip)에 의한 마찰진동이 발생할 수 있으며 이 경우 베어링 구조물을 포함한 추진축계 시스템의 자려진동이 발생할 수 있으므로 이에 대한 주의가 필요하다.
이 연구에서 다루는 함정에서 발생한 축계 진동이 베어링 마찰에 의한 진동인지 여부를 확인하기 위해서 이상소음이 크게 발생하는 PCL 35 조건에서 함 선회 시 진동 변화를 계측하고 체감적으로 이상소음 발생여부를 평가하였다. 체감평가로부터 선회를 시작하면 발생하던 이상소음이 사라짐을 알 수 있었다.
Fig. 3은 함 선회 운전 시 함미 스트러트 상부지지 구조 선체의 진동 변화를 보여주고 있다. Fig. 3에서와 같이 진동 스펙트럼에서 f0 Hz의 진동은 함 선회와 상관없이 계속 남아있으나 f1 Hz 및 이들 조화성분은 함 선회 시 사라짐을 확인할 수 있었으며 함 선회 완료 후 다시 직진 항해 시 이상소음이 다시 발생하며 f1 Hz 및 이의 조화성분 진동이 다시 크게 발생함을 알 수 있었다.
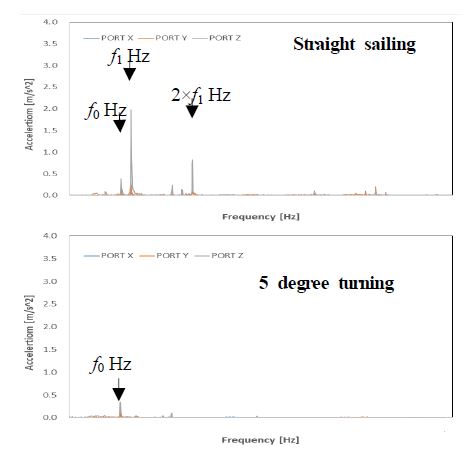
Variation of the acceleration measured on the hull plate supported to the strut at PCL 35 when the ship is turning
따라서 선회 시험 결과로부터 이 연구에서 다루는 함정에서 발생하는 진동은 추진축계 비선형 마찰진동으로 인한 스틱슬립 현상으로부터 발생하고 있음을 강하게 예측할 수 있었다.
3. 수윤활베어링-추진축 간 스틱슬립 진동
일반적으로 베어링과 축간의 비선형 진동은 베어링과 축의 상대운동만을 고려한 단순 모델을 가지고 설명되고 있다(1,3,5). 따라서 이 장에서는 4장에서 다루어질 이상소음의 원인분석을 위한 공학적 근거로 단순모델을 이용하여 이상소음 발생 메카니즘을 다루고자 한다.
이 연구에서는 Fig. 4와 같이 해수윤활 베어링과 추진축을 2자유도 모델로 가정하여 축과 베어링에 대한 운동방정식을 식 (1)과 같이 정의하였다.
(1) |
여기서 I는 축의 질량관성모멘트, θ는 축의 각 변위, q은 베어링의 직선변위, ct는 축의 회전방향 댐핑, kt는 축의 회전방향 강성, m은 베어링의 질량, c는 베어링의 댐핑계수, k는 베어링의 강성, F는 마찰력, R0은 축반경, μd는 축-베어링간 등가 마찰계수, N은 베어링에 작용하는 수직력이다.
마찰계수-회전속도 곡선의 기울기가 음수를 가지는 경계 또는 혼합 윤활 영역에서 등가 마찰계수(μd)는 식 (2)와 같이 축과 베어링의 상대속도의 항으로 표현된다(1).
(2) |
여기서 μ0는 베어링-축간의 동마찰계수, μ1는 베어링-축간의 정마찰계수, a는 상수, 은 축-베어링 간 상대속도이다.
따라서 식 (1) 우항의 마찰력을 마찰에 의한 감쇠계수(c')와 축-베어링 간 상대속도의 항으로 표현할 수 있으며() 좌항의 감쇠항과 동일한 형태로 표현할 수 있다. 여기서 식 (1) 우항의 축계 마찰력항의 감쇠계수(c')가 좌항의 진동 시스템 감쇠계수(c)보다 클 경우 전체 등가 진동 시스템의 감쇠계수를 음수로 만들 수 있다. 이 경우 마찰 외의 다른 외력이 가해졌을 때 축과 베어링의 변위응답은 감쇠하는 것이 아니라 발산하는 불안정한 계가 된다. 또한 이러한 발산하는 진동은 축 및 베어링 계의 고유진동수에서 발생하므로 이러한 진동의 형태를 마찰에 의한 스틱슬립 비선형 자려진동이라고 한다(1,3,5).
따라서 이 절에서는 식 (1)의 추진축계 모델에 대해 저속에서 마찰계수가 식 (2)의 형태를 가질 때 축계가 불안정한 계가 되어 자려진동을 할 수 있음을 수학적으로 기술하고자 한다.
진동이 사라지고 안정화된 이후 축 및 베어링의 응답을 θ* 및 q*라 두면 이는 식 (3), (4)와 같다.
(3) |
(4) |
여기서 Ω는 축 회전수이다.
및 를 식 (5)와 같이 정적변위를 제거한 순수한 진동 변위로 정의하고 이를 이용하여 식 (1)의 운동방정식을 다시 정리하면 운동방정식은 식 (6), (7)과 같이 나타낼 수 있다.
(5) |
(6) |
(7) |
여기서 F'는 진동력이 제거된 안정상태에서의 마찰력이다.
식 (6), (7)에서 마찰계수-회전속도 곡선의 기울기가 음수일 때 우항의 진동 마찰력 항은 식 (2)의 마찰계수 식을 이용하여 식 (8)과 같이 나타낼 수 있다.
(8) |
식 (8)에서 Taylor 급수전개를 이용하여 를 선형화하면 식 (9) ~ (11)과 같이 나타낼 수 있다.
(9) |
(10) |
(11) |
여기서 정적인 힘은 무시하여((0,0)=0) 식 (9)를 재정리하면 외력항은 식 (12)와 같이 단순하게 정리할 수 있다.
(12) |
따라서 식 (12)를 식 (6), (7)의 미분방정식에 대입하여 재정리하면 식 (13) ~ (15)와 같다.
(13) |
(14) |
(15) |
식 (13) ~ (14)의 해를 라 두면 식 (13) ~ (14)는 식 (16)과 같이 나타낼 수 있다.
(16) |
여기서 고유해를 구하기 위한 특성방정식은 식 (17) ~ (21)과 같다.
(17) |
(18) |
(19) |
(20) |
(21) |
일반적으로 식 (13), (14) 미분방정식의 일반해는 축 및 베어링의 변위로 식 (22)와 같이 나타낼 수 있다.
(22) |
여기서 t는 시간, D1, D2, D3, D4 는 상수, ai + jbi 는 i 차 고유진동수, 는 i 차 고유벡터이다.
식 (22)에서 축 및 베어링의 변위 고유치의 실수부(a1, a2)가 양의 값을 가질 경우, 즉 식 (17)의 특성방정식의 모든 계수인 C1, C2, C3, C4가 모두 양수가 아닐 때 해당 고유치를 가지는 고유진동수에서 시스템 변수인 축 및 베어링 진동 변위인 및 는 발산하게 되어 큰 자려진동이 발생하게 된다(9). 이와 같이 축-베어링 간 스틱슬립이 발생하게 되면 축계 시스템은 불안정한 계가 되어 계의 고유진동수에서 자려진동을 할 수 있음을 알 수 있다.
4. 진동 계측 결과 분석
이 연구에서 다루는 추진축계의 V-스트러트 및 I-스트러트의 경우 수윤활 베어링을 사용하고 있으며 라인베어링, 추력베어링 및 감속기어 베어링은 모두 오일베어링을 사용하고 있다. 수윤활 베어링 사용 시 전절의 이론적 검토결과와 같이 윤활막이 충분히 형성되지 않은 마찰윤활 및 경계윤활 조건인 저속구간에서 베어링 반력이 증가하여 마찰력이 커질 경우 마찰진동 및 이로 인한 자려진동이 발생할 수 있다.
이 연구에서 다루는 함정의 경우 축의 특정 회전수에서 이상소음이 발생되며 이상소음의 형태는 특정 주파수(f1 Hz) 및 이의 조화 성분이다. 이 주파수는 회전수 변화에 따라 달라지지 않으며 축의 회전수와 전혀 관계가 없는 특이 주파수이다. 또한 이 주파수에서의 소음은 함 선회 시 함 위치 변경으로 인해 바로 사라졌다가 직진 항해 시 다시 발생하기를 반복된다. 함 선회조건에서 이상소음의 변화는 함 선회로 인한 함 위치 변경 시 베어링 접촉조건이 변경되고 이로 인해 추진축의 마찰에 의한 자려진동 발생조건이 변화했기 때문으로 판단된다. 이를 검증하기 위해 시간신호분석 및 DEMON 분석을 통해 이상진동이 마찰에 의한 것인지를 파악하고자 하며 V-스트러트 지지 구조부의 고유진동 계측을 통해 이상소음 발생 시 나타나는 f1 Hz 진동의 발생원인을 찾아보고자 한다.
4.1 시간 주파수 신호 분석
이상소음이 크게 발생하는 조건 중 PCL 40 계측 조건에서 Fig. 5와 같이 진동 계측을 위해 속력을 맞추었을 때 최초 이상소음이 없다가 측정 시작 후 약 34초가 지날 때 갑자기 이상소음이 급격히 증가하는 특이한 현상이 발생하였다. 이러한 형태는 전형적인 비선형 자려진동의 형태이다. 비선형 자려진동 발생조건에서는 시스템이 불안정한 계(unstable system)가 되며 시간에 따라 진동응답이 감소하는 것이 아니라 증가하기 때문에 이러한 현상이 발생하게 된다.
Fig. 6은 이때의 진동 스펙트럼의 컨투어(contour) 다이어그램이다. Fig. 6과 같이 이상소음 발생 시 V-스트러트 지지부 상부선체의 진동 스펙트럼에서 f1 Hz 및 이 주파수의 조화 성분 주파수의 진동이 크게 발생함을 알 수 있다. 따라서 시간 주파수 신호 분석 결과로부터 발생되는 진동의 형태가 비선형 마찰에 의한 스틱슬립 진동의 형태임을 알 수 있었다.
4.2 DEMON 분석
DEMON(detection of envelop modulation on noise) 기법은 마찰이나 유동 등에 의해 발생한 고주파 광대역 신호가 특정 주파수에 동조 되는지를 파악하는 기법으로 힐버트 변환(Hilbert transform)을 통해 동조되는 신호의 포락선을 찾고 그 포락선이 어떠한 주파수성분을 가지는지 분석하는 기법이다. Fig. 7은 PCL 40 조건에서 마찰이 주로 발생되는 1.0 kHz ~ 7.4 kHz의 주파수 범위에서 좌, 우현 함미 스트러트 지지 선체의 진동 신호에 대한 DEMON 분석 결과이다.
Fig. 7로부터 이상소음이 크게 발생하는 좌현의 경우 DEMON 스펙트럼에서 f1 Hz 및 이들 조화성분이 뚜렷하게 나타나며 BPF 성분 및 이들 조화성분 또한 저주파영역에 현저하게 나타나고 있음을 알 수 있으나 이상소음이 없는 우현의 경우 BPF 성분 및 이들 조화성분외 특이 성분이 없음을 알 수 있다.
일반적으로 베어링 마찰은 축과 베어링 간 상대운동으로 인해 발생 될 수밖에 없다. 일반적으로 함 운항 시 추진축계에서는 블레이드 통과주파수 성분의 변동추력 발생으로 인해 추진축의 변동 굽힘 모멘트를 발생시키므로 이를 지지하는 베어링의 마찰력 변화를 야기 시키며 이로 인해 마찰에 의한 고주파 광대역 진동은 축회전수 및 블레이드 통과 주파수에 동조되어 발생한다. 여기서 스틱슬립에 의한 비선형 마찰진동이 발생할 경우 추진축계 시스템은 불안정계가 되어 베어링을 포함한 추진축계 구조물의 고유진동수를 가진하게 되므로 고주파 광대역 마찰 진동은 축회전수, 블레이드 통과주파수 뿐만 아니라 이들 고유진동수와 동조되어 나타나게 된다.
따라서 좌현의 진동 신호에 대한 DEMON 스펙트럼에서 f1 Hz가 추진축계 시스템의 고유진동수라고 가정하면 이는 비선형 스틱슬립에 의한 마찰진동에 의한 형태임을 알 수 있다.
따라서 f1 Hz 주파수가 어떤 구조물의 고유진동수인지 확인하기 위해서 추가적으로 모드 시험을 수행하였다.
4.3 Modal 분석
주파수 분석 및 DEMON 분석결과로부터 이상소음 발생 시 발생하는 f1 Hz에 대한 정의를 위해서 V-스트러트 베어링 부착 구조물에 대한 모드 시험을 수행하였다. 모달 시험은 함을 상가한 상태에서 V-스트러트 베어링 하우징 및 주변 구조물에 대해 수행하였다. 상가 시 확인 결과 스트러트 베어링에 연결되어 있는 로프가드에 Fig. 8과 같이 균열이 발생되어 있음을 알 수 있었다. 여기서 로프가드는 함미부 V-스트러트 베어링 하우징에 용접되어 있는 외팔보 형태의 구조로 15 mm 두께의 강판으로 구성되어 있으며 공진 발생 시 소음 발생이 쉬운 구조임을 알 수 있었다.
따라서 로프가드의 진동으로 인해 이상소음이 발생하고 이 때문에 균열까지 발생되었을 가능성을 파악하기 위해 로프가드에 대한 진동해석을 수행하였다. 진동해석은 MSC. nastran/patran을 가지고 수행하였다. Fig. 9는 로프가드 진동해석을 위한 FEM 모델이다. 로프가드는 2D quadrilateral mesh(노드점 : 4점)를 사용하여 모델링 하였으며 로프가드 끝부분은 로프가드가 스트러트 베어링 하우징에 용접되어 있으므로 RBE2 요소를 이용하여 연결부를 가상의 한 노드점으로 연결한 후 이 노드점을 완전 구속시켰다. 또한 로프가드는 물속에 잠겨 있기 때문에 접수효과에 따른 부가수 질량 효과를 구현하기 위해서 nastran MFLUID 기능 사용하였다.
로프가드 해석에 적용한 물성치는 Table 1과 같다.
Table 2는 공기 중 및 부가수 효과를 고려한 수중에서의 로프가드의 고유진동수 해석결과이다. 부가수 효과를 고려할 경우 로프가드의 고유진동수는 공기 중 고유진동수 대비 대략 1.44배 ~ 1.72배 정도 감소(부가수 질량으로 인해 로프가드 전체 질량이 2.1배 ~ 3.1배 증가)함을 알 수 있었으며 해석 결과 1, 2차 고유주파수(f1 Hz)가 이상소음 발생 시 나타나는 이상진동 주파수와 일치함을 알 수 있다. Fig. 10(a)는 수중에서 로프가드의 1차 ~ 3차 고유모드를 보여주고 있다. 일반적으로 실린더 구조물은 1차 모드가 타원형 모드를 가지나 한 쪽 끝단이 구속되어 있을 경우 Fig. 10(a)과 같이 여러 개의 절점을 가지는 형태의 고유모드를 가지게 된다. Fig. 10(a)와 같이 주요모드들이 실제 파손이 발생한 지점인 구멍이 있는 지점을 중심으로 변형하는 모드임을 알 수 있다. Fig. 10(b)는 1차 ~ 3차 모드에서의 응력 분포이며 실제 균열이 발생한 구멍 주변에서 가장 큰 응력이 발생됨을 알 수 있다. 따라서 이 해석 결과로부터 이 연구에서 다루는 함정에서 발생하는 이상소음의 주요주파수인 f1 Hz는 로프가드의 고유진동수로 강하게 추정되었으며 이 진동으로 인해 로프가드의 균열까지 발생하였을 가능성이 충분히 있다고 판단되었다. 따라서 이 연구에서 다루는 함정의 상가 시 로프가드의 고유진동수를 모드 시험을 통해 해석결과와 비교 하였다. 모드 시험은 로프가드의 수직방향 한 지점에 3축 가속도계를 부착하고 시계방향으로 45°씩 이동하여 로프가드 자유단부와 구속부에 대해서 각각 8지점씩 총 16지점에 로프가드 원통면에 수직방향으로 임팩트해머를 이용하여 임팩트 입력을 가하여 수행하였다.
실험을 통해서 임팩트 입력에 대한 16지점의 가속도 응답의 주파수 응답 함수를 Fig. 11과 같이 구하고 이를 이용하여 로프가드의 고유진동수 및 고유모드를 추출하였다.
계측결과 고유진동수는 Table 3과 같으며 수중에서의 접수효과에 따른 부가수 질량을 고려했을 때의 고유진동수는 해석결과를 바탕으로 공기 중 고유진동수의 1.59배(1차 ~ 20차 고유진동수의 fa /fw 평균값) 작게 예측하였다. 계측결과 고유진동수는 해석결과보다 다소 작계 계측되었으나 3차 모드가 수중에서 약 f1-2 Hz의 고유 진동수를 가질 것으로 예상됨에 따라 실제 이상소음 발생 시 나타나는 f1 Hz 진동성분의 주파수와 매우 유사함을 알 수 있었다. Fig. 10(a)에서 3차 모드의 경우도 1차 모드와 진동형태가 유사함을 알 수 있었다. 로프가드의 경우 항해 중 접근이 불가하기 때문에 부가수 질량 효과에 따른 고유진동수 변화는 정확히 파악하기는 어렵다. 따라서 정확한 고유진동수 보다는 근사적인 값으로 평가할 수밖에 없고, 어느 정도 주파수의 오차를 고려하여 평가할 수밖에 없으며, 근사적으로 평가해 보았을 때 이상소음 발생 시 이상진동의 주파수는 로프가드의 고유진동수일 가능성 매우 큰 것으로 판단되었다. 구조물에 균열이 발생한 상태에서 진동력이 가해지면 강성이 떨어져 균열 발생 전 대비 더 큰 진폭으로 진동할 수 있으므로 상가 시 균열부를 용접하고 항해 시운전을 통해 이상소음 변화를 추가적으로 계측해 보았다.
4.4 로프가드 수리 후 진동 계측 결과 분석
4.1절 ~ 4.3절의 계측 결과로부터 로프가드의 파손은 축과 V-스트러트 베어링 간에서 발생한 스틱슬립 마찰진동에 의해 베어링지지 구조물을 포함한 추진축계가 불안정 계가 되고 베어링 구조물들 중 외팔보 구조로 지지된 로프가드가 자려진동을 하면서 파손된 것으로 추정되었다.
또한 로프가드의 균열로 인해 로프가드의 공진현상이 증폭되고 이로 인해 이상소음이 발생된 것으로 예측하였다. 따라서 로프가드의 균열부를 절단하고 여기에 강판을 용접하여 수리를 진행한 후, 항해 시운전을 통해 이상소음의 변화를 진동계측을 통해 확인해 보았다. 진동계측은 함 출항 후 PCL 30 ~ 60 속력 조건에서 계측하였다.
Fig. 12은 이상소음이 크게 발생했던 구간인 PCL 35 ~ PCL 55에 대한 진동 스펙트럼이다. Fig. 12에서 좌측 그림(conventional)은 로프가드 수리 전, 우측 그림(proposed)은 로프가드 수리 후 진동 스펙트럼이다. Fig. 12에서와 같이 시험 결과 기존에 발생하던 이상소음은 로프가드 수리 후 거의 발생하지 않았으며 진동 스펙트럼에서 f1 Hz 및 이들 조화 성분이 모두 사라졌음을 알 수 있었다. 항해 중 PCL 35 ~ PCL 55에서 f2 Hz (= f1-8.0 Hz)의 작은 피크 성분이 회전수와 관계없이 발생하였으며 이는 f1 Hz 성분이 항해조건에 따른 로프가드의 부가수 질량 변화 및 균열수리에 따른 구조물의 특성 변경으로 인해 달라진 것으로 추정되었다.
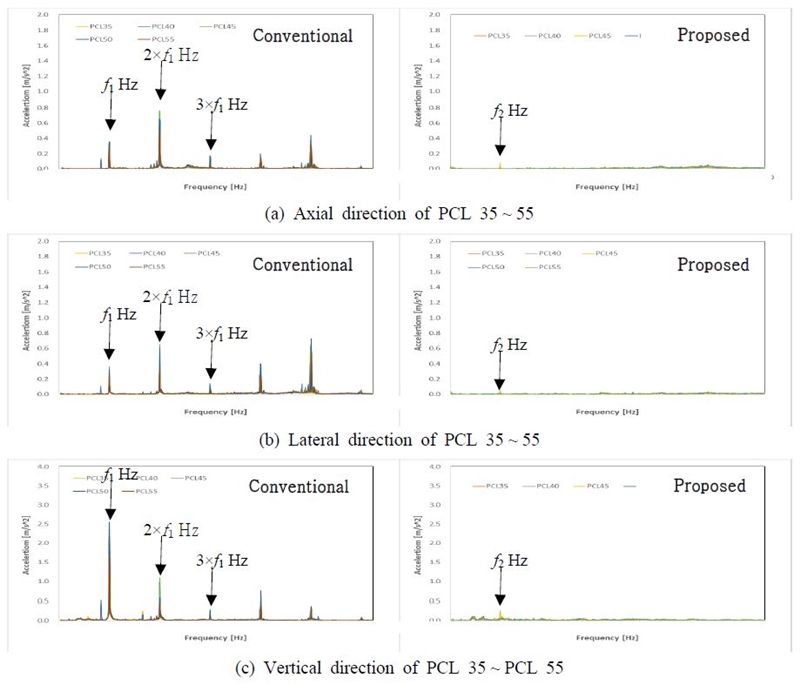
Spectra of the acceleration on the aft hull supporting the V-strut according to the speed variation measured after departure(conventional : before repairing, proposed : after repairing)
이상소음 및 특이진동 성분은 기존 측정값에 비해서는 매우 감소함을 알 수 있었으나 계측 이후 계속적으로 시운전을 수행해 본 결과 함 운항 조건에 따라 일부 소음이 증가하기도 함을 알 수 있었다. 시험결과와 같이 항해 중 항해조건에 따라 이상소음이 발생한다는 것은 로프가드에 자려진동이 발생한다는 증거이고, 이러한 현상이 반복되게 되면 다시 로프가드에 균열이 발생되며 이로 인해 이상소음이 더 증폭될 것으로 예측되었다. 따라서 로프가드의 두께증가 및 구조보강을 통해 자려진동이 발생하는 로프가드의 고유진동수를 늘리고 이를 통해 진동 가속도의 진동 진폭을 낮추는 등의 개선이 필요할 것으로 판단된다.
5. 결 론
이 연구에서 다루는 함정의 PCL 35 ~ PCL 55에서 함미 좌현부에서 발생하는 이상소음은 진동계측 결과로부터 V-스트러트 베어링의 마찰에 의한 스틱슬립 비선형 진동에 의해 발생하는 것으로 예측되었다. 통상 마찰에 의한 스틱슬립 비선형진동은 자려진동의 형태로 나타나며 베어링 구조물을 포함한 추진축계 시스템의 고유진동수에서 큰 진동이 발생하게 된다.
이 연구에서 다루는 함정의 경우 f1 Hz 및 이들 조화성분의 진동으로 인해 이상소음이 발생하고 있으며 고유진동 해석 및 모드 시험 결과 이 성분은 로프가드의 고유진동수로 추정되었다.
실제로 로프가드 균열이 발생한 이후 이 소음이 크게 발생하였고, 로프가드 균열 수리 후 시운전에서 이상소음이 급격히 저감됨을 확인함에 따라 이상소음은 로프가드의 자려진동에 의해 발생된 것으로 강하게 추정된다.
이상소음 저감 및 로프가드 균열 방지를 위해서는 로프가드의 강성 보강을 통해 진동진폭을 줄이는 방법이 적용되어야 할 것으로 판단되며 이를 위해 로프가드 두께 증가, 보강재 추가 등의 대책이 필요할 것으로 판단된다.
Acknowledgments
이 연구는 해군본부로부터 지원받은 “20-운용함정 소음진동 점검 연구용역”을 통해 얻어진 결과입니다.(계약번호 제 2020UMM0347호)
References
-
Simpson, T. A. and Ibrahim, R. A., 1996, Non Linear Friction Induced Vibration in Water-lubricated Bearings, Journal of Vibration and Control, Vol. 2, No. 1, pp. 87~113.
[https://doi.org/10.1177/107754639600200106]
-
Bhushan, B., 1980, Stick-slip Induced Noise Generation in Water-lubricated Compliant Rubber Bearings, Journal of Lubricant Technology, Vol. 102, No. 2, pp. 201~210.
[https://doi.org/10.1115/1.3251470]
-
Peng, E., Liu, Z., Zhou, X., Tian, Y. and Zhao, M., 2012, Study on Nonlinear Friction-induced Vibration in Water-lubricated Rubber Stern Tube Bearings, The Open Mechanical Engineering Journal, Vol. 6, pp.140~147.
[https://doi.org/10.2174/1874155X01206010140]
- Albers, A. and Herbst, D., 1998, Chatter-causes and Solutions, The 6th LuK Symposium, Luk GmbH & Co, Germany, pp. 23~45.
-
Han, H. S., Lee, K. H., Park, S. H. and Jeon, S. H., 2018, Investigation for the Mechanism and Main Parameters of the Stick-slip Nonlinear Friction Induced Vibration in Water-lubricated Stern Tube Bearing, Transaction of the Korean Society of Noise Vibration Engineering, Vol. 28, No. 6, pp. 655~663.
[https://doi.org/10.5050/KSNVE.2018.28.6.655]
-
Hirani, H. and Verma, M., 2009, Tribological Study of Elastomeric Bearings for Marine Propeller Shaft System, Tribology International, Vol. 42, No. 2, pp.378~390.
[https://doi.org/10.1016/j.triboint.2008.07.014]
-
Zhimin, Y., Xincong, Z., Hongling, Q., Wanying, N., Hao, W., Kai, L. and Yumin, T., 2015, Study on Tribological and Vibration Performance of a New UHMWPE/graphite/NBR Water Lubricated Bearing Material, Wear, Vol. 332-333, pp.872~878.
[https://doi.org/10.1016/j.wear.2014.12.054]
-
Wang, H., Liu, Z., Zou, L. and Yang, J., 2017, Influence of Both Friction and Wear on the Vibration of Marine Water Lubricated Rubber Bearing, Wear, Vol. 376-377, pp. 920~930.
[https://doi.org/10.1016/j.wear.2017.02.006]
- Rao, S., 2011, Mechanical Vibrations 5th Edition, Prentice Hall, Chap. 2.
Hyungsuk Han received a B.S. in Production and Mechanical Engineering from Pusan National University in 1996. He then went on to receive his M.S. and Ph.D. degrees in Mechanical Engineering from Pusan National University in 1998 and 2007, respectively. Dr. Han is currently a Senior Researcher at Defense Agency for Technology and Quality, Busan, Korea.
Soohong Jeon received a B.S. in Production and Mechanical Engineering from Pusan National University in 2007. He then went on to receive his M.S. and Ph.D. degrees in Mechanical Engineering from Pusan National University in 2009 and 2014, respectively. Dr. Jeon is currently a Senior Researcher at Defense Agency for Technology and Quality, Daejeon, Korea.
Cheongwon Lee received a B.S. in Mechanical Engineering from Dong-A University in 2007. Mr. Lee is currently a Senior Researcher at Defence Agency for Technology and Quality, Daejeon, Korea.
Yonghoon Kim received a B.S. in Mechanical Engineering from Pusan National University in 2009. Mr. Kim is currently a Researcher at Defence Agency for Technology and Quality, Daejeon, Korea.