
전기자동차 스플라인 품질과 축 불균형에 의한 충격성 소음 개선에 대한 연구
© The Korean Society for Noise and Vibration Engineering
Abstract
Impact noise generated in electric vehicles in the 200 Hz ~ 500 Hz is perceived as rumble noise of an internal combustion engine. It is one of the biggest noise problems during electric vehicle development. This noise is caused by a shock phenomenon generated in each revolution due to interference between the minor diameter of the motor shaft spline and the reducer input shaft spline due to misalignment. Through spline measurement comparisons and spline LDP analysis results, the minor diameter of the motor shaft and its misalignment have proved to be important factors. To eliminate spline impact noise and maintain the spline's major and minor diameter stably, a hobbing manufacturing method has been developed and adapted for the motor spline. Finally, this impact noise has been improved by 10 dBA or more in electric vehicles successfully.
Keywords:
Impact Noise, Rumble Noise, Electric Vehicle, Motor, Reducer, Spline, Major Diameter, Minor Diameter, Hobbing키워드:
충격성 소음, 럼블성 소음, 전기자동차, 모터, 감속기, 스플라인, 대경, 소경, 호빙1. 서 론
전기차는 배터리의 전기를 이용하여 모터를 회전시켜 차량의 구동력을 얻는다. 전기차의 구동모터는 높은 출력과 회전력을 만들고 감속기는 모터의 회전수를 필요한 수준으로 저감하여 더 높은 회전 토크를 얻을 수 있도록 조정하는 역할을 한다. 모터는 작동하자마자 최대 토크가 발생하여 기존의 내연기관 대비 중저속 조건에서 가속력이 뛰어나고 배터리가 차체 하단에 탑재되어 무게중심이 낮아 선회성이 우수하며, 가감속 안정성도 좋다.
기존의 내연기관 차량에 비해 전기차의 구동계는 단순하지만, 소음진동 측면에 대한 개발 요구는 상대적으로 증가하고 있다. 이는 크게 두 가지 요인에 의해 기인되는데, 내연기관이 없기 때문에 연소음에 의한 마스킹(masking) 효과가 없어서 실내 소음이 조용해진 것과 전기차에 대한 소음 진동 특성 측면에서 개발이 확립되지 않았다는 것이다.
차량에서 울리는 듯한 소음 특성을 가진 럼블성 소음은 기존의 내연기관에서는 엔진 크랭크 샤프트의 굽힘과 비틀림 진동 현상이 실린더 블록에 영향을 미쳐서 발생하는 약 200 Hz ~ 500 Hz 대역의 소음이었다(1~3). 그러나 전기차는 엔진이 없음에도 불구하고 운전 조건에 따라 주파수 대역과 청감 특성상 럼블성 소음처럼 인지되는 소음이 발생하기도 한다.
일반적인 전기차는 모터에서 감속기로 동력을 전달하기 위하여 스플라인 연결을 이용한다. 스플라인 연결은 키홈보다 많은 치를 이용하여 좀 더 우수한 내구성을 가진다. 스플라인은 원주방향의 거동이 없으며 외경과 내경 스플라인 간에 일정량의 각도 불일치와 축방향의 상대적인 슬라이딩 등을 허용하기 때문에 회전 기계 분야에서 광범위하게 사용하는 요소이다. 스플라인 결합에서 관찰되는 가장 일반적인 고장은 가공, 조립, 그리고 운전 조건 등에 따라서 발생하는 표면 마모, 부식 피로, 치 파손 등이 있다.
이러한 스플라인 결합에 대한 연구들은 수치해석적 접근법으로 유한요소법을 이용하거나, 치접촉면에 의도적인 리드 크라우닝을 주거나, 스플라인 정렬 불일치와 스플라인 제조 품질 등에 따른 치의 인덱싱 에러 등에 따른 하중 분포 영향성 등을 연구한 사례들이 있다. 최근에 발표된 연구에는 전기차에서 발생하는 럼블성 소음의 원인을 모터와 감속기 결합시 구성되는 축정렬과 모터 스플라인부의 피치에러가 지배인자라고 기술하고 있다(4~8).
그러나, 앞서 언급한 스플라인 피치에러가 전기차에서의 럼블성 소음의 근본적인 해결책을 제시하지는 못하였다. 따라서 스플라인 결합에 따른 상호 치 접촉 관계와 부하 분포, 관련 메커니즘 등의 상관관계 등을 정확하게 파악하지 못하면 스플라인부의 고장 메커니즘을 이해하는 것은 제한적일 수밖에 없다.
이 논문은 스플라인 결합으로 구성된 전기차에서 럼블성 소음의 근본 원인을 확인하고, 스플라인부의 제원 조사결과와 스플라인 엘디피(spline LDP) 프로그램을 이용하여 상관성을 검증하고 관리항목을 개발하여 럼블성 소음의 품질 안정화 방안을 마련한 것을 기술하였다.
2. 본 론
2.1 현상
Fig. 1은 스플라인 결합으로 구성된 전기차에서 주행중에 발생하는 럼블성 실내 소음과 모터와 감속기에서 측정한 진동 데이터를 나타낸 것이다. 전기차에서 약 200 Hz ~ 500 Hz 대역 사이에서 발생하는 럼블성 소음을 유발하는 진동은 Fig. 1과 같이 모터와 감속기 연결부에서 가장 크게 나타나는 것을 확인할 수 있으며 Fig. 2와 같이 모터 1회전당 1회의 타음성 현상이 발생되는 것을 확인하였다. 이 현상은 모터와 감속기 결합시 회전하면서 발생하는 정렬 특성에 따라 영향을 받는 것으로 추정되며, 회전수가 증가함에 따라 빠르게 반복되는 타음성 소음 현상이 럼블성 소음처럼 인식된 것이다. Fig. 3은 동일한 차량과 동일한 차속조건에서 전기차의 회생제동 조건에 따라 럼블성 소음 발생 여부를 보인 것이다. 무부하 조건인 ‘Lv0’ 조건과 작은 토크가 걸리는 ‘Lv1’ 회생제동 조건에서는 소음이 발생하지 않지만, 상대적으로 큰 토크가 걸리는 ‘Lv2’ 조건에서는 소음이 발생하였다. 즉 토크에 따라 스플라인부 축정렬이 영향을 받는다는 것을 확인한 것이다.
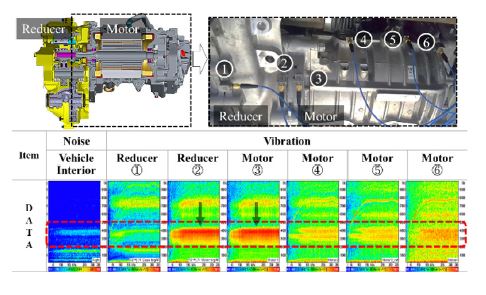
A rumble noise phenomena and measurement data of the electric vehicle (creep condition, 35 s) (X axis : time(s), Y axis : frequency(Hz))
Fig. 4는 동일한 차량에서 모터와 감속기를 조립하는 기준핀 체결 위치를 변경하면서 계측한 것이다. 기준핀은 모터와 감속기의 축정렬과 체결 강성을 확보하는 기준이 되는 것으로 기준핀의 체결 위치를 변경함에 따라, 제조 품질과 조립 품질 등에 따라 축정렬과 체결 강성이 영향을 받아 럼블성 소음이 발생하는 조건이 바뀌는 것을 확인할 수 있다. 이를 통하여 축정렬이 럼블성 소음에 영향을 미치는 인자 중 하나임을 확인하였다.
2.2 측정 데이터 분석
2.1절에서 언급된 조건과 현상들을 종합하면 럼블성 소음은 모터에서 감속기로 동력을 전달하는 과정에서 모터샤프트와 감속기의 인풋샤프트 스플라인부 사이에서 발생하는 충격음으로 모터가 회전하면서 섭동하는 스플라인부에 가해지는 하중 조건과 축 정렬의 변화에 따라서 소음이 발생한다는 것을 확인하였다.
이러한 기본 현상 연구를 통하여 주요 인자를 찾기 위해 소음이 발생한 모터와 감속기의 주요 요소에 대한 제원 조사를 실시하였다. 특히 스플라인부를 구성하는 형상 요소 중 조립, 축 정렬, 회전, 섭동 등과 같은 조건에서 소음을 유발시킬 수 있는 영향 인자 등을 조사하였다.
Fig. 5는 모터샤프트와 감속기 인풋샤프트의 스플라인 결합부 단면도를 나타낸 것이고, Fig. 6은 모터샤프트를 3차원 측정하여 스플라인부의 대경(major diameter)과 소경(minor diameter), 단일 치 두께, 치간 편차(distance deviation between over pin center), OPD(over pin diameter) 등의 예를 나타낸 것이다.
Table 1은 모터 스플라인부의 설계치와 기존 제작기법인 전조(rolling)공법에 의한 샘플, 소음 발생품과 호빙(hobbing)공법에 의한 샘플을 측정한 결과를 보인 것이다. 기본적으로 소음 발생품은 대경과 소경의 크기가 스펙 범위를 넘어서는 것을 확인할 수 있으며, 전조품 중 소음 양호품은 소경이 큰 것을 확인할 수 있으며 호빙품이 설계치에 가장 가까운 것을 확인할 수 있다.
2.3 스플라인 엘디피 분석
스플라인 엘디피(spline LDP(load distribution program))는 스플라인(spline)의 하중 분배 모델을 구현한 것으로 순수 비틀림 하중이나 스퍼어, 헬리컬 기어 등이 축 외부에 장착되어 하중이 가해지는 조건 등을 포함한 다양한 하중 조건에서 스플라인부의 하중 분포를 특성화하여 분석할 수 있다. 뿐만 아니라, 정렬 불량 및 치 수정 등이 스플라인 하중 분포에 미치는 영향과 제조 오차의 영향성 등을 확인하고 예측할 수 있는 프로그램이다. Fig. 7은 스플라인 엘디피를 실행한 예를 보인 것이다(9).
Fig. 8은 스플라인 엘디피 프로그램으로 스플라인 설계 제원을 기본으로 하여 Table 1의 측정 결과 중 베이스품과 소음 발생품의 모터 샤프트와 감속기 인풋샤프트 스플라인부의 측정 결과를 기초로 분석한 결과와 실제 제품의 단면을 잘라서 비교한 것이다. 이를 통하여 해석과 실제 제품 모두에서 소음 발생품이 모터 스플라인부의 소경부와 감속기 스플라인부의 대경부에서 일정한 수준의 간극이 없는 것을 확인할 수 있다.
2.4 스플라인 엘디피를 이용한 영향성 분석
2.1절, 2.2절, 2.3절을 통하여 스플라인부가 럼블성 소음의 발생 위치인 것을 확인하였고, 축정렬과 스플라인부의 대경, 소경 간섭 등이 소음에 영향을 미친다는 것에 대한 확인이 이루어졌다.
특히 축정렬에 영향을 미치는 인자 중에는 조립 오차, 동심도 오차와 스플라인 치의 피치에러(인덱스에러) 등이 있다. 특히, 이러한 여러 인자들 중 가장 영향을 미치는 인자에 대한 조사와 분석을 통하여 기준을 수립하고 관리하는 것이 필요하다. 이를 검증하기 위하여 Table 2와 같이 제조 환경 조건에서 발생할 수 있는 최대 크기 수준의 미스얼라인먼트와 동심도 에러값 등을 기준으로 스플라인엘디피 분석을 실시하였다. Table 2는 차량에서 소음 문제가 발생하는 조건인 크립(creep) 주행 10 Nm, 20 %이상 경사로를 오르는 200 Nm 조건, 그리고 실제 발생한 축정렬 불량의 한계인 0.1° 불량과 동심도 에러 0.136 mm 등을 나타낸 것이다.
Fig. 9는 스플라인 양산품의 치사이의 인덱스 에러를 도시한 것으로 전조공법과 호빙공법으로 제작한 양산품을 측정한 일반적인 수준의 인덱스 에러 데이터와 생산하면서 발생할 수 있는 최대한의 크기로 약 100배 정도 큰 인덱스 에러를 부여한 것을 나타낸 것이다.
Fig. 10은 스플라인 엘디피를 이용하여 스플라인부의 최대 접촉하중을 분석한 것으로 Fig. 10(a)와 Fig. 10(b)는 각각 10 Nm의 저부하 조건과 200 Nm인 고부하 조건에서 기본제원, 전조 공법 샘플, 소음 발생품, 호빙 공법 양호품의 측정값을 이용하고 Table 2의 정렬 에러와 중심도 에러 등을 반영하여 해석한 것을 비교한 것이다. Fig. 10(a)와 Fig. 10(b)에서 보여진 것과 같이 축정렬 에러가 어느 정도 영향을 미치는 것을 확인할 수 있다. 그러나, 스펙을 벗어나지는 않는 수준이다. 전조공법의 소음발생품의 대경과 소경 차이가 스펙을 벗어나는 수준으로 영향을 미치는 것을 확인할 수 있다. 또한 Fig. 10(a)와 Fig. 10(b)를 비교해 보면 10 Nm와 200 Nm 수준의 적용 토크는 영향이 상대적으로 작음을 알 수 있다.
Fig. 10(c)와 Fig. 10(d)는 각각 Fig. 10(a)와 같은 조건에서 전조 공법과 호빙 공법 샘플에서 축정렬이 있는 조건에서 일반적인 수준의 치간 인덱스 에러를 반영하여 분석한 것이다. 이를 통하여 현재 양산하는 수준에서의 치간 인덱스 에러는 럼블성 소음 발생에 영향을 미치는 인자가 아닌 것으로 판단할 수 있다.
Fig. 10(e)와 Fig. 10(f)는 각각 Fig. 10(a)와 같은 조건에서 전조 공법과 호빙 공법 샘플의 치간 인덱스에러를 현재 생산하면서 발생할 수 있는 최대 수준인 약 100배 크게 반영하여 분석한 것이다. 이러한 조건에서도 인덱스 에러의 영향이 상대적으로 작은 것을 확인할 수 있다. 결과적으로, 생산하면서 발생할 수 있는 스플라인 인덱스 에러는 기본적으로 영향을 미치지만, 실제 소음 문제를 유발할 정도의 수준은 아니며, 축정렬 에러와 스플라인의 대경부와 소경부 직경 에러가 동시에 발생했을 때, 가장 큰 영향을 미친다.
2.5 검증
Fig. 11은 스플라인 엘디피 분석을 통하여 확인한 자료를 기초로 하여 모터 샤프트 대경부와 소경부의 값을 측정하고 비교하여 스플라인의 대경부와 소경부에서 간섭이 발생하지 않도록 선정한 샘플로 검증한 결과이다.
Fig. 11(a)와 같이 개선전에는 실내소음이 46 dBA 수준이었고 진동이 108 dB 수준이었으나, Fig. 11(b)와 같이 개선후에는 차량 실내에서 소음은 인지가 되지 않는 35 dBA 수준이고, 진동은 92 dB 수준으로 소음이 11 dBA 진동이 16 dB 이상 개선되었다(9).
2.6 품질관리
Fig. 12는 모터 샤프트의 대경부와 소경부의 관리 기준과 측정 결과를 보인 것이다. 개선 전의 수준과 개선 후의 품질 수준을 비교해 보면 개선 후에 설계 기준안에서 안정적으로 유지 관리되는 것을 확인할 수 있다. 이러한 품질을 유지하기 위하여 모터 샤프트 스플라인부 제조 공법을 전조 공법에서 호빙 공법으로 변경하였으며 특히 소경부를 주요 관리항목으로 지정하고 일정한 품질이 유지될 수 있도록 정기적인 점검 방법과 가공툴의 유지 보수 등을 강화하였다.
3. 결 론
이 연구에서는 전기차를 개발하는 과정에서 발생한 200 Hz ~ 500 Hz 대역의 충격성 소음을 근본적으로 개선한 연구 결과를 기술한 것으로 다음과 같은 결론을 얻었다.
(1) 스플라인 결합의 전기차에서 발생한 200 Hz ~ 500 Hz 대역의 소음은 소음 발생 음색과 분석 특성에 따라 럼블 소음이라고 언급되었으나, 실제 현상은 모터 샤프트와 감속기 인풋샤프트 스플라인부의 섭동 현상 중에 축정렬과 모터 샤프트 소경부의 크기에 따른 걸림감에 의해 1회전마다 발생하는 타음성 현상이다.
(2) 소음 발생품과 양호품의 측정결과와 스플라인 엘디피를 이용하여 분석하고 실제 제품의 확인 검증 등을 통하여 축정렬과 모터 샤프트의 스플라인 소경부 간섭이 가장 큰 영향 인자임을 확인하였다. 뿐만 아니라, 일반적인 양산 수준의 치간 인덱스 에러는 큰 영향을 미치는 인자가 아님을 확인하였다.
(3) 모터 샤프트 스플라인 소경부 크기 품질을 일정하게 생산하기 위하여 가공 공법을 전조 공법에서 호빙 공법으로 변경하고 소경부 크기에 대한 품질 규제를 강화하였다. 이를 통하여 전기차에서 소음을 10 dBA 이상 개선하였다.
(4) 주요 인자들의 기준 검증과 설정, 가공 공법 변경, 업체 품질관리 방법 등을 구체적으로 수립하여 스플라인부에 의한 충격 소음 발생의 근본 원인을 제거하였다.
References
- Lee, J. K. and Yeo, S. D., 1997, The Characteristics of Engine Noise and Its Reduction Techniques, Journal of KSNVE, Vol. 7, No. 4, pp. 689~700.
- Lee, S. K., Kim, B. S. and Park, D. C., 2004, Development of Rumbling Index and Its Identification, Proceedings of the KSNVE Annual Spring Conference, pp. 997~1002.
-
Baek, J. S., An, K. H., Shin, T. J., Lee, S. K., Han, D. H., Jin, J. M. and Jung, I. S., 2020, Identification of Rumbling Noise in a Passenger Car using Blocked Forced Transfer Path Analysis, Transactions of the Korean Society for Noise and Vibration Engineering, Vol. 30, No. 3, pp. 294~302.
[https://doi.org/10.5050/KSNVE.2020.30.3.294]
-
Hong, J., Talbot, D. and Kahraman, A., 2014, Load Distribution Analysis of Clearance-fit Spline Joints using Finite Elements, Mechanism and Machine Theory, Vol. 74, pp. 42~57.
[https://doi.org/10.1016/j.mechmachtheory.2013.11.007]
-
Hong, J., Talbot, D. and Kahraman, A., 2014, A Semi-analytical Load Distribution Model for Side-fit Involute Splines, Mechanism and Machine Theory, Vol. 76, pp. 39~55.
[https://doi.org/10.1016/j.mechmachtheory.2014.02.002]
-
Hong, J., Talbot, D. and Kahraman, A., 2015, Effects of Tooth Indexing Errors on Load Distribution and Tooth Load Sharing of Splines under Combined Loading Conditions, Journal of Mechanical Design, Vol. 137, No. 3, Article No. 032601.
[https://doi.org/10.1115/1.4029282]
-
Hong, J., Talbot, D. and Kahraman, A., 2016, A Stiffness Formulation for Spline Joints, Journal of Mechanical Design, Vol. 138, No. 4, Article No. 043301.
[https://doi.org/10.1115/1.4032631]
-
Ha, T. W., Huh, J. W., Choi, S. K., Min, D. W., Chae, C. K., Abdy, A., Schmitt, C., Mahmoud, H., Jain, S. and Rodrigues, L., 2020, Robust Development of Electric Powertrain NVH for Compact Electric SUV, SAE Technical Paper, Article No. 2020-01-1503.
[https://doi.org/10.4271/2020-01-1503]
- Lee, H. K., Kim, M. S., Moon, H. S. and Yoo, D. K., 2021, A Study on the Development of Rumble Noise for Electric Vehicle, Proceeding of the KSNVE Annual Autumn Conference, p. 85.
Hyun Ku Lee is a NVH global R&D master engineer in the Hyundai - Kia Motors Research and Development Division. He received his B.S. and M.S. degrees of Mechanical Engineering from The Konkuk University in 1995 and in 1997 respectively. He won a Jang Young-sil Award in 2010 and won the 1st Yang Bo Suk Technical Award in 2016 from the KSNVE. He developed several 6th, 8th speed ATs, a CVT, and transmission error measurement equipment for external gear and planetary gear sets and a pRMC, a PTA program for gear designer and also authored several papers related to the automatic transmission and reducers noise. His current research on driveline’s noise focused on the planetary gear NVH and efficiency, EOL, transmission error, total backlash, electric vehicle reducer and In wheel motor NVH and so on.